The BMS defines the making and breaking point of your electric vehicle. It takes more than a battery to keep it on road.
With everyday growing concerns over the depreciating health of our ecosystem, we need to adopt sustainable approaches. Vehicular pollution being one of the major contributors, the switch to electric vehicles is more of a need than a want. Electrified transportation is the most viable way to achieve the green dream for the whole world. In the coming future, hybrid electric vehicles, plug-in hybrid electric vehicles, and pure battery electric vehicles will be dominating the roads.
Electric vehicles have traction motors instead of an internal combustion engine, which makes them more efficient. As EVs run on batteries, it is of utmost importance that they are managed well. Well-managed batteries mean a well-managed vehicle. Batteries installed in an electric vehicle should not only provide long-lasting energy but also provide high power. The battery capacity range for an electric vehicle is about 30-100 KWH or more. EVs have a large number of battery cells which require an efficient battery management system (BMS). Lead-acid, lithium-ion and nickel-metal hydride are the used traction batteries, out of which lithium-ion batteries are the most used ones. Li-ion batteries are highly reactive, smaller in weight, and have the highest energy. The chemical structure, solid electrolyte, and stable encapsulation make it suitable for applications prone to mechanical vibrations and impacts. The charging and discharging of lithium-ion batteries is faster than other batteries. Hence, a Battery management system is used which allows the battery to operate within its safety zone.
Benefits of the battery management system
BMS is pivotal in an EV because the batteries should not get overcharged or over-discharged. This could lead to damage to batteries, rise in temperature which reduces the life span of the battery, and in worst-case scenarios, can endanger the life of the driver and passengers. BMS prompts service and caution. It helps in maximizing the range of the vehicle by optimizing the amount of energy stored in it. A battery management system provides the necessary data to algorithms that decide the battery’s overall health. It detects and reacts to ground faults. BMS takes various sensor readings of your vehicle and monitors the data. The BMS must be able to cope with the complex nature of power batteries, such as high capacity, high power, wide temperature variation, and harsh driving conditions.
Components of the battery management system
BMS has some main blocks such as a charger, battery packs, master unit, slave unit, protection unit, and cooling system. The master unit controls the charging, discharging, heating, and cooling of the battery pack. Saves calibration data, and serves the state of charge (SoC) measurement and state of health (SoH) maintenance. The Slave unit monitors cells in series for temperature, and voltage and performs active and passive cell balancing for each cell. It derives power from the cells being monitored. The charger provides a constant current voltage charging circuit. The charging circuit charges the battery based on control signals from the master unit. The battery pack consists of all the cells connected in parallel and series combinations. Battery packs usually have 12 cells in series. The protection unit consists of the main relay, pre-charge relay, and fuse to protect the battery pack from overcurrent, over-voltage, and under-voltage conditions. When unwanted conditions occur, the relay will sense and isolate the battery pack from the load. The load for the battery pack will be the vehicle motor. The cooling system will maintain the surrounding temperature of the battery pack. The master unit sends signals to the cooling system.
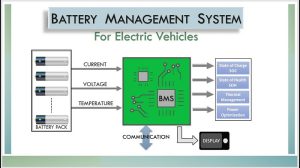
Applications of the battery management system
The complexity of a BMS depends on the application. The primary goal it serves is to keep the battery operating in its safety zone. Charging control is an essential feature of the BMS. Batteries are more frequently damaged by inappropriate charging than by any other cause. Another important feature of BMS is state-of-charge determination. It signals the user and controls the charging and discharging process.
State-of-health determination reflects the general condition of the battery and its ability to deliver the specified performance in comparison to a fresh battery. SoH can be determined from the measurement of either cell impedance or cell conductance.
Cell balancing compensates weaker cells by equalizing the charge on all cells in the chain to extend the battery life. When charging, weak cells may become overstressed and eventually fail which can cause the battery to fail prematurely. To solve this issue, BMS incorporates cell balancing to equalize the cells and prevent individual cells from becoming overstressed.
Logbook function – as SOH is relative to the condition of the new battery, a measurement system must hold a record of the initial conditions for comparison.
The choice of the communications protocol is not determined by the battery but by the application of the battery. The BMS in an EV must communicate with the upper vehicle controller and motor controller to ensure proper operation.
A proper battery management system is vital to the proper functioning of an EV. if the battery is not managed well, the vehicle will not be running on the road for a long time.