Anton Paar, a distinguished company specializing in the development, production, and distribution of precision laboratory instruments and process measuring systems, alongside delivering customized automation and robotic solutions, has established itself as a leader in electrical and mechanical testing of EV batteries. In an exclusive interview with Himanshu Vaibhav, a Technology Journalist from timesEV.com, Mr Prasad Gosavi, Technical Manager at Anton Paar India, provided comprehensive insights into the initiatives undertaken by testing companies to standardize battery pack testing procedures, covering both electrical and mechanical aspects.
TimesEV: What are the key challenges encountered by testing engineers during the execution of mechanical and structural properties testing for electric vehicle batteries?
Prasad Gosavi: India is an emerging market for electric vehicles and is expected to expand at a compound annual growth rate of over 90% in the current decade. The battery is a principal component in the EV and presently mainly Lithium-ion battery is powering the EVs.
Many automotive testing and certifying agencies have been working towards standardization tests for battery safety, and electrical and mechanical tests of the battery packs. However, battery raw material’s performance check remains a black box for OEMs and vehicle manufacturers. They often rely on the supplier’s report about raw material quality. Electric cars are almost 30% heavier as compared to conventional ICE cars. The major contributor towards the heavier weight of EVs is the battery pack.
A typical Lithium-ion battery consists of electrodes, separators and electrolytes. These solid components are made out of raw materials in powders and particle form. Hence a challenge remains to understand the physical, chemical and performance properties of these raw materials. This understanding will lead towards optimizing battery performance, reduction of the EV weight and further extension of the EV’s driving range.
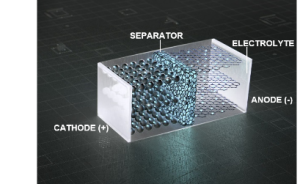
TimesEV: Provide comprehensive information regarding the testing equipment utilized in lithium-ion battery raw material testing.
Prasad Gosavi: As mentioned, the primary raw material for Lithium-ion battery components is in the form of solid powders and powders in general are highly porous. Such porosity is expected in the powders for the transfer of ions from the anode towards the cathode and the other way around, during the battery operation. Typical powder properties such as the density of these solids, particle size, porosity and available surface area for ion transfer need to be studied to optimize the component performance.
A separator is a typical polymeric porous membrane that acts as a barrier between the anode and cathode and at the same time allows transportation of Li-ions from one side to another, during operation. Measuring the pore size of the separator and its mechanical properties is essential.
Anton Paar offers comprehensive instrument solutions for battery raw materials studies. NOVA system performs measurements to determine the surface area of electrode powder. PoreMaster system based upon mercury intrusion porosimetry allows studies related to porosity present in the solid powder as well as porous separators. Ultrapyc 5000, a gas pycnometer system measures the density of electrode slurries as well as solid powders. Additionally, MCR 702, a versatile system performs dynamic mechanical analysis of the separator under applied mechanical load conditions and the viscosity of the electrode slurries. The powder particle size is monitored with PSA
Advanced measurements of the battery cell in the form of a pouch or prismatic cell, are performed on the XRDynamic 500 system for understanding the structural changes during charging–discharging.
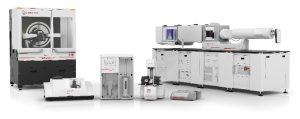
TimesEV: Provide detailed information about the mechanical tests that assess the battery electrode and separator’s capability to withstand the mechanical forces that can arise during a battery operation.
Prasad Gosavi: An electrode is a two-component system consisting of a solid base film with slurry coating on the base. The base substrate is made of metal (aluminium or copper) and over it, a coating of active material either lithium metal oxide or graphite is applied. During the battery operation, the electrode as well as the separator, goes through tension and torsion forces that can potentially tear these components. Determination of mechanical resistance to tension, tear, and torsion of the separator and electrode material via dynamic mechanical analysis (DMA) to determine the forces that the separator/electrode can withstand before breaking or tearing. These mechanical strength test on the separator or electrode is performed via Anton Paar MCR 702 system. The right combination of strength and porosity of separator membranes is important to improve electrical resistance and physical stability and to prevent short circuits.
TimesEV: Provide a concise summary of the mechanical testing conducted on electric vehicle battery electrodes.
Prasad Gosavi: Additionally, a mechanical test needs to be performed to study the adhesion of the coating on the electrode substrate. The quality and durability of the battery depend both: on the type of electrode coating and on its adhesion to the electrode itself; an increase in coating adhesion can increase the capacity of the battery. The determination of the adhesion of the active layers on electrodes is therefore important for the development of high-capacity batteries.
TimesEV: Provide comprehensive information about the procedure involved in conducting testing for battery electrode slurries.
Prasad Gosavi: Proper design and development of the mixing and coating processes of the anode and cathode slurry is an essential part of battery performance. The determination of flow properties such as viscosity, can help to find just the right mixing procedure to identify the ideal coating process. Knowing the rheological behaviour of a slurry can furthermore help with dimensioning slurry pumps or predicting slurry storage behaviour. Uniform thickness and density of the slurry layer are crucial to ensure the battery’s lifetime, charge-discharge performance, and ion transfer rate – independent of the battery’s size. Additionally, the determination of the percentage of solid material in slurries is crucial to define the quality and homogeneity of the final coating. Tests to determine the particle size and surface charge of additives used to improve battery conductivity are performed on Anton Paar Litesizer 500 and the PSA system.
TimesEV: Provide a succinct overview of the test employed to estimate the battery’s performance and useful life across multiple charging and discharging cycles.
Prasad Gosavi: X-ray diffraction (XRD) is a common test performed for studying the battery materials as it allows non-destructive, in-situ or -operando investigations of the material properties and structural changes in batteries during charging, discharging or storage. Such studies can be performed on a wide variety of battery types e.g., cylindrical cells, pouch cells, and prismatic cells.
These in-operando measurements allow changes in the battery materials to be observed in real-time during the charging and discharging process. Anton Paar XRDynamic 500 with its outstanding capabilities is the perfect tool for the battery as well as electrochemical investigation.