STMicroelectronics has introduced its fourth-generation STPOWER silicon carbide (SiC) MOSFET technology, delivering breakthroughs in power efficiency, density, and robustness for automotive and industrial applications. Designed to optimize EV traction inverters, the technology enhances energy efficiency and performance in both 400V and 800V platforms, driving the adoption of more affordable and sustainable electric vehicles. Additionally, it addresses critical needs in renewable energy, industrial motor drives, and data centers, reflecting ST’s commitment to advancing electric mobility and industrial efficiency through innovation and a vertically integrated manufacturing strategy.
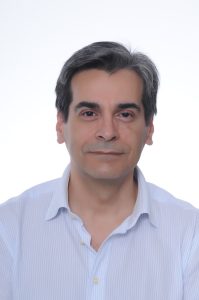
Rashi Bajpai, Sub-Editor at ELE Times, engaged with Gianfranco Dimarco, Chief of Staff and Marketing Communication Manager Power & Discrete at STMicroelectronics, to explore emerging SiC MOSFET technology.
ELE Times: What are the key advantages of the new 750V and 1200V SiC MOSFET devices for mid-size and compact EVs, and how will they contribute to making electric vehicles more affordable and accessible?
Gianfranco Dimarco: STMicroelectronics’ new 750V and 1200V SiC MOSFET devices offer significant advancements for mid-size and compact electric vehicles, enhancing efficiency, reducing size and weight, increasing range, and enabling faster charging. The improved efficiency stems from SiC MOSFETs’ ability to minimize switching losses, significantly reducing energy waste during driving. Additionally, the compact and lightweight design of these components optimizes space utilization, boosting vehicle performance and extending the distance covered on a single charge. Their higher power capacity also facilitates faster charging, making electric vehicles more practical for daily use. Together, these innovations lower production costs, accelerating the adoption of green technologies in the automotive industry.
ELE Times: Can you provide specific performance metrics or benchmarks that demonstrate the improvements in efficiency, power density, and robustness of the Generation 4 SiC MOSFETs compared to previous generations or silicon-based alternatives?
Gianfranco Dimarco: The 4th generation SiC MOSFETs feature several key advancements over the previous generation:
- Faster Switching Speeds: this results in lower switching losses, which is crucial for high-frequency applications, enabling more compact and efficient power converters.
- Lower On-Resistance (RDS(on)): significantly reduced on-resistance minimizes conduction losses and enhances overall system efficiency.
- Enhanced Robustness: improved performance in Dynamic Reverse Bias (DRB) conditions, exceeding the AQG324 automotive standard, ensuring reliable operation under harsh conditions.
- Smaller Die Size: the average die size of Generation 4 devices is 12-15% smaller than that of Generation 3, considering an RDS(on) at 25 degrees Celsius. This allows for more compact power converter designs, saving valuable space and reducing system costs.
ELE Times: What can you share about the timeline and expected features of the forthcoming fifth-generation SiC power devices? How does the planned radical innovation differ from current technologies in terms of performance and application?
Gianfranco Dimarco: The main goals for the 5th generation of SiC MOSFET include achieving higher power density, further reducing on-resistance (RDS(on)), and improving thermal performance. These advancements aim to meet the increasing demands of high-power applications in automotive, industrial, and renewable energy sectors. We will share more details on Gen5 and the planned radical new technology at the appropriate time.
ELE Times: With STMicroelectronics’ vertically integrated manufacturing strategy, how does the company plan to ensure a resilient supply chain for SiC components to meet growing global demand, especially for automotive and industrial markets?
Gianfranco Dimarco: STMicroelectronics ensures a resilient supply chain for SiC components through its vertically integrated manufacturing strategy. The company is investing in facilities like the Silicon Carbide Campus in Catania, a fully vertically integrated SiC substrate manufacturing facility, which is expected to start production in 2026. This approach allows STMicroelectronics to control the entire production process, from raw materials to finished components, ensuring consistent quality and supply. Additionally, strategic investments to start the migration from 150mm to 200mm for SiC, further enhance manufacturing efficiencies and scalability. By vertically integrating and expanding its manufacturing footprint, STMicroelectronics is well-positioned to meet the growing global demand for SiC components, especially in the automotive and industrial markets.
ELE Times: Which leading EV manufacturers are currently collaborating with STMicroelectronics to implement the Generation 4 SiC technology into their vehicles, and what feedback have they provided regarding the anticipated performance improvements?
Gianfranco Dimarco: Leading EV manufacturers and Tier 1s are engaged with ST to integrate Generation 4 SiC technology into their vehicles and powertrain solutions. We will share more details on our customers at the appropriate time.
ELE Times: Beyond EV traction inverters, how does the Generation 4 SiC technology enhance the performance of high-power industrial applications, such as solar inverters, energy storage systems, and data center power supply units?
Gianfranco Dimarco: STMicroelectronics’ Generation 4 SiC technology not only advances EV traction inverters but also plays a crucial role in enhancing high-power industrial applications like solar inverters, energy storage systems, and data center power supply units. Solar inverters benefit from increased efficiency and higher power density, resulting in better energy conversion and more reliable solar power systems.
Energy storage systems also leverage SiC devices for greater durability and efficiency, making them ideal for long-term use, particularly in grid balancing and hybrid power systems with renewables. In data centers, SiC technology ensures stable, efficient power delivery, preventing disruptions in critical operations. These advancements underscore the growing importance of SiC technology in modern high-power industrial applications, significantly improving both efficiency and reliability across various sectors.
ELE Times: What can you share about the timeline and expected features of the forthcoming fifth-generation SiC power devices? How does the planned radical innovation differ from current technologies in terms of performance and application?
Gianfranco Dimarco: The main goals for the 5th generation of SiC MOSFET include achieving higher power density, further reducing on-resistance (RDS(on)), and improving thermal performance. These advancements aim to meet the increasing demands of high-power applications in automotive, industrial, and renewable energy sectors. We will share more details on Gen5 and the planned radical new technology at the appropriate time.
ELE Times: How does STMicroelectronics’ vertically integrated manufacturing strategy contribute to its sustainability goals, and what specific initiatives are in place to ensure environmentally friendly production processes for these new SiC devices?
Gianfranco Dimarco: Through our vertically integrated manufacturing strategy we maintain full control over the entire production chain, from raw materials to finished products, and all initiatives are aligned with our sustainability strategy and our sustainable manufacturing commitment, in terms of energy consumption and greenhouse gas emissions, air, and water quality.
All these initiatives. ST Sustainability Report 2024