Author: STMicroelectronics
The X0115ML is our first compact silicon control rectifier (SCR) for ground fault circuit interrupters (GFCIs) and arc-fault circuit interrupters (AFCIs) that can withstand a surge peak off-state voltage of 750 V. Additionally, its small SOT23-3L package (2.75 mm x 3.10 mm) makes it the smallest thyristor on the market today. Engineers can thus gain significant space while providing a repetitive peak off-state voltage of 600 V for industrial applications. Moreover, its 1.1 mm creep age distance meets the UL 840 requirements for 120 V AC insulation without coating.
Table of Contents
- Why design industrial GFCIs and AFCIs?
- X0115ML and what to look for in the silicon control rectifier that will go in an industrial GFCI or AFCI?
Why design industrial GFCIs and AFCIs?
It’s a matter of life and death
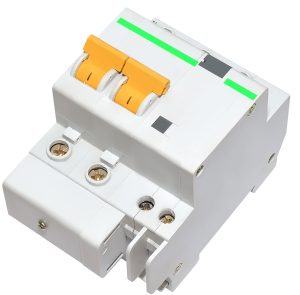
According to the 2021 US Bureau of Labor Statistics survey on fatal occupational injuries (the latest year on record), out of the 798 fatalities caused by exposure to harmful substances or environments, exposure to electricity is the second leading cause of death (152) after exposure to harmful substances (551). Put simply, electrocution is a real risk for plant workers and employees working in an industrial setting, especially if there’s water. The reason is that even a “small” current of 10 mA can cause a severe shock, and 50 mA can produce enough muscle contraction to stop the heart or induce respiratory distress.
It’s to prevent electrocution
To protect people, the US National Electrical Code started requiring GFCIs in residential installations and wrote new regulations in 2000 for high-voltage industrial settings (480 V to 600 V). Most are familiar with the traditional GFCI in circuit breakers. The system monitors the current at the hot and neutral lines to determine if the electricity going out of a socket goes back in. If both levels are equal, then all is well. If there’s an unbalance, the system assumes the electricity is going somewhere else, like through a person being electrocuted. In that event, the GFCI trips the circuit between the hot and neutral lines to interrupt the current flow.
It’s to prevent electrical fires
On the other hand, AFCIs protect against electrical fires by monitoring arc forms and arcing amplitudes to detect dangerous conditions. Consequently, AFCIs are electronically more complex than GFCIs. An arc fault may result from loose or overheated wires or a current flowing through an unintended object. All these events will generate a high-intensity and massive surge in temperature, which, if left unchecked, will start an electrical fire. Corrosion or liquids can also cause an arc fault, which can have severe consequences in an industrial setting.
It’s to create smarter factories
Beyond the national regulations that govern such products, makers are also designing smarter GFCIs and AFCIs by connecting them to the cloud, collecting more data on power consumption, and automating them. Resetting a circuit breaker remotely is hugely beneficial when trying to streamline maintenance. However, these features demand a lot more electronics, from microcontrollers to radios, sensors, and more. Hence, the new GFCIs and AFCIs must pack drastically more components on the same surface area as the previous models, which means that engineers looking to increase the overall density of their designs are on the hunt for smaller components. However, given the critical nature of the product, they cannot sacrifice performance or robustness for a smaller package.
X0115ML and what to look for in the silicon control rectifier that will go in an industrial GFCI or AFCI?
Trigger Gate Current
The first technical characteristic many look for in the SCR that will be at the centre of their GFCI or AFCI is its gate sensitivity. Traditionally, devices for industrial settings must not be too sensitive, or they will cause nuisance tripping, meaning that the protection device will think there’s a fault when there isn’t. The reason is that as the application uses significantly more power, normal current variations are larger than in devices designed for residential use. With its gate trigger current ranging between 30 µA and 150 µA, the X0115ML is sensitive enough to work in all applications while still being compatible with an industrial environment.
Surge peak voltage
Another key metric is its surge peak off-state voltage because it will determine the thyristor’s robustness. Indeed, to be effective, the SCR must deal with very high voltage spikes, especially in an industrial setting. Traditionally, while devices for high power systems have a surge peak off-state voltage of 700 V, the X0115ML climbs to 750 V. Consequently, engineers enjoy greater headroom and can use the ST device in more settings. Moreover, we also included greater protections against EMI to increase its robustness over its life span.
Package size and overall footprint
Finally, size is an increasingly critical metric because of the proliferation of smart circuit interrupters that necessitate more electronics. Usually, SCRs used for industrial GFCIs, and AFCIs use an SOT-223 package. Hence, by moving to a SOT-23-3L, we can reduce the overall footprint by a factor of 5 without compromising performance or the UL 840 requirements. The X0115ML is even smaller than our X0115MUF, which has an identical gate trigger current and direct voltage surge but uses an SMBflat-3L packaging measuring 5.6 mm x 3.05 mm.
Read the full article at https://blog.st.com/x0115ml/